EXTENSÔMETROS COLÁVEIS DE RESISTÊNCIA ELÉTRICA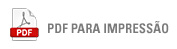
>> INFORMAÇÕES TÉCNICAS
FATOR DE SENSIBILIDADE (Gage Factor)
Extensômetros elétricos são transdutores. Isto é, convertem uma grandeza que se quer medir, em outra, que se pode medir mais facilmente.
No caso, convertem uma deformação ε, que se quer medir, numa variação de resistência elétrica, a ser medida de forma mais acessível.
Detalhando melhor: convertem uma variação de comprimento em relação a um comprimento inicial ε = Δ L / L, numa variação de resistência elétrica em relação a uma resistência inicial Δ R / R.
Este fator de conversão é conhecido como FATOR DE SENSIBILIDADE do extensômetro (gage factor), sendo expressado por:
FATOR DE SENSIBILIDADE = (ΔR/R) / (ΔL/L) = (ΔR/R) / ε
O Fator de Sensibildade depende, assim, do material com que é feito o condutor elétrico do extensômetro.
Sendo este material a liga metálica constantan, o Fator de Sensibilidade é sempre 2,1, que é o que ocorre na linha de extensômetros elétricos da EXCEL SENSORES.
Caso a utilização dos extensômetros elétricos seja a produção de outros transdutores daí derivados, como transdutores de força (células de carga), de pressão, de torque, etc, o Fator de Sensibilidade, embora presente, não altera o processo de sua fabricação e utilização.
Caso a utilização dos extensômetros elétricos seja em extensometria, alguns instrumentos de leitura, mas não todos, apresentam o recurso de se poder regular o “ganho” do aparelho pelo Fator de Sensibilidade do extensômetro, permitindo que também seja utilizado com extensômetros de outros materiais. Neste caso, fornecemos o valor do Fator de Sensibilidade do extensômetro ao lado da identificação do seu lote, pois ele varia de lote para lote, apenas na sua segunda casa decimal.
TAMANHOS E FORMAS GEOMÉTRICAS DOS EXTENSÔMETROS
Conceitos fundamentais sobre a atuação dos extensômetros orientam a nossa compreensão e raciocínio para a sua escolha, face a diversidade de tamanhos e formas geométricas existentes.
Quanto ao tamanho:
O extensômetro mede a deformação do local onde está aplicado pela variação de sua resistência elétrica. Como esta resistência ocupa uma determinada área, formada pelo comprimento e largura de sua grade, é sob esta área que ele irá “captar” a deformação. Supondo-se que em diferentes pontos desta área houver deformações diferentes, para a área completa, a variação de resistência elétrica corresponderá à deformação média nela ocorrida.
Isto, de certa forma, explica porque se tem extensômetros de tamanhos (e áreas) muito diversos, sendo que alguns, de tão pequenos, tendem a se aproximar do tamanho de um ponto. Por outro lado, existem materiais muito heterogêneos, onde também se pretende medir deformações. Exemplos clássicos são rochas e concreto. A heterogeneidade é tal que se o extensômetro for muito pequeno não se lê nada representativo. Tem-se, portanto, a necessidade de extensômetros grandes, cuja área leve a uma deformação média que considere como homogêneo o material que, na nossa visão normal, é heterogêneo.
Outro fator a ser considerado é a própria dimensão da peça, e nela, do local a ser analisado, que muitas vezes nos conduz ao tamanho do extensômetro que é possível utilizar.
É bom destacar que, para extensômetros muito pequenos a sua manipulação torna-se mais difícil, e muito mais precisa e rigorosa deve ser a sua localização na peça, onde um pequeno desvio pode significar que ele está num outro ponto fora do desejado.
Quanto à forma:
O extensômetro é feito para medir só as deformações que ocorrem ao longo de seu eixo principal, isto é, no sentido longitudinal da grade. Assim sendo, ele é seletivo na indicação das deformações. Esta propriedade nos obriga a identificar previamente em que sentido deverão ocorrer as deformações no local em estudo. E a utilização deverá ser, em princípio, de um extensômetro unidirecional.
Mas, se o objetivo são deformações situadas a 45° do eixo da peça, provocadas por esforços de torção ou cisalhamento, existem os modelos unidirecionais a 45° , à direita ou à esquerda, e os modelos espinha de peixe, que são duplos, 45° à direita e à esquerda ao mesmo tempo.
Por vezes pretende-se determinar as deformações principal e secundária de uma peça, situadas uma da outra a 90°. Para tanto existem as rosetas duplas a 90°.
E quando não se sabe qual é o sentido da deformação principal, pode-se utilizar do princípio de medir-las em 3 direções diferentes, em ângulos pré-definidos entre si, extraindo-se a resultante pelo Círculo de Mohr. Assim existem os modelos de roseta tripla a 90° e 120°.
Existem também extensômetros voltados para aplicações específicas, como os modelos diafragma, que captam deformações existentes em formas tal como um “fundo de copo”, quando o mesmo está instalado numa tubulação submetida à uma pressão interna, que provoca a deformação da membrana deste “fundo de copo”, daí resultando um sensor de pressão.
EXTENSÔMETROS AUTO-COMPENSADOS
Os extensômetros são sensores que colados num local e conectados à instrumentação apropriada passam a indicar as deformações deste local, a partir de um instante inicial. Com estas informações afere-se as forças aplicadas e as tensões envolvidas.
Entretanto, se no local também houver variações de temperatura, haverá também a correspondente deformação térmica, de dilatação ou contração, cuja indicação se somará às deformações mecânicas, que, normalmente, são exclusivamente as que nos interessam.
É nesse sentido que existem extensômetros que, aproximadamente, auto-compensam, por si só, dentro de uma faixa de temperatura, as deformações
térmicas correspondentes a um determinado coeficiente, e as leituras assim feitas passam a se referir apenas às deformações mecânicas. São os extensômetros auto-compensados, cuja auto-compensação, portanto, refere-se a um determinado coeficiente de dilatação térmica. Comercialmente, entretanto, estão restritos a apenas alguns coeficientes , como seja, 11 ppm/oC (06 ppm/oF), correspondendo a aços em geral e concreto, 16 ppm/oC (09 ppm/oF), correspondendo a várias composições de aço inoxidável, e 23 ppm/oC (13 ppm/oF) , correspondendo ao alumínio.
Origina-se, desta forma, a designação corriqueira de “extensômetro para aço”, ou “para inox”, ou “para alumínio”.
ENSAIOS EM TEMPERATURA ACIMA DA AMBIENTE
Os extensômetros EXCEL, constituídos com base de poliymida e grade metálica de constatan, em sua configuração básica, sem os opcionais de pontos de solda em seus terminais, ou fios a ele soldados, podem ser utilizados em temperaturas até 175°C, podendo chegar a 200°C.
Para temperaturas superiores, os extensômetros são de outros materiais para base e grade, apresentando características diferentes, e não fazem parte da nossa linha de fabricação.
Os pontos de solda, executados nos terminais dos extensômetros, ou nas conexões necessárias, para a fixação dos fios condutores elétricos, em liga eutética com 63% de estanho e 37% de chumbo, suportam a temperatura máxima de 120°C, excepcionalmente um pouco mais, já com a solda se tornando pastosa, pois se liquefaz a 183°C. Razão esta que também limita a 120°C a temperatura de utilização dos extensômetros EXCEL que apresentam pontos de solda em seus terminais, isto é, as opções “S” e “L”.
Existem outras composições de solda que se fundem a temperaturas superiores, chegando a 310°C, na liga com 1% de estanho, 97,5% de chumbo, e 1,5% de prata. Evidentemente, as dificuldades de soldagem também aumentam, a começar pela temperatura do ferro de solda.
Referindo-nos ao elemento fixador utilizado no extensômetro, se seu princípio ativo for cianoacrilato, a temperatura não deve ser superior a 90°C , no máximo 100°C. Se for o KBR-610, da EXCEL, esta temperatura máxima pode chegar a 260°C.
Resumindo:
• Até 90°C (máximo 100°C)
– Extensômetros: qualquer opção
– Fixador: cianoacrilato ou KBR-610
• Até 120°C (máximo 130°C)
– Extensômetros: excluir as opções que apresentem pontos de solda nos terminais. Estas soldas só deverão ser feitas após a fixação do extensômetro, uma vez que não suportam a temperatura do processo de aplicação do KBR-610.
– Fixador: KBR-610
• Até 175°C (máximo 200°C)
– Extensômetros: excluir as opções que apresentem pontos de solda nos terminais. Estas soldas só deverão ser feitas após a fixação do extensômetro, com a utilização do KBR-610, tendo-se o cuidado de selecionar como ligas de solda aquelas cuja fusão sejam adequadas à temperatura pretendida.
– Fixador: KBR-610
• Acima de 175°C
– Extensômetros: especiais
PREPARAÇÃO DA SUPERFÍCIE E FIXAÇÃO DO EXTENSÔMETRO NA PEÇA
É fundamental que o extensômetro, para reproduzir fielmente todas as micro-deformações ocorridas na superfície da peça, esteja integralmente e firmemente aderido a esta superfície, durante todo o tempo em que durar o ensaio ou a utilização da estrutura que se está instrumentando.
Para tanto, a superfície local precisa estar corretamente preparada e receptiva, e essa fixação ser feita de modo adequado. Dai vem a importância da preparação da superfície bem como da fixação do extensômetro na peça.
Vários são os materiais em que se torna necessário medir deformações e nela
aplicar os extensômetros. Mencionamos alguns, como diversos tipos de aços carbono, de aços inoxidáveis, de ligas não ferrosas (como o bronze), o concreto, a rocha, materiais compósitos, madeira, ossos. Para todos aplica-se o conceito acima exposto. Mas a preparação da superfície e a fixação deve-se adequar a cada caso.
Apenas como ilustração e exemplo, o texto prossegue atendo-se a alguns materiais, mas principalmente em sua aplicação em aços carbono, em sua condição mais ampla e rigorosa.
PREPARAÇÃO DA SUPERFÍCIE DA PEÇA
O que primeiro chama a atenção é que a preparação da superfície não implica apenas na remoção de impurezas as mais grosseiras, como camadas de tinta ou graxa, revestimentos por galvanoplastia, etc., mas de micro impurezas que muitas vezes são imperceptíveis a olho nu. Destas destacam-se oxidação, umidade, pequenas partículas de poeira e películas de gordura, que não devem se interpor entre o extensômetro e a peça.
Se cuidados não forem tomados, é freqüente a contaminação da superfície por gorduras, provenientes das próprias mãos do aplicador. Muitas vezes, o aplicador pode até seguir as recomendações quando da aplicação dos primeiros extensômetros, mas depois, talvez por julgar excessivos os cuidados com contaminações que ele nem vê, deixa de cumpri-las com o mesmo rigor. Assim, estes cuidados devem ser obedecidos como a um verdadeiro ritual.
A primeira regra a ser seguida é que o operador deve lavar as mãos, com sabão neutro, antes da aplicação do extensômetro, principalmente antes da preparação final da superfície, e lava-las novamente sempre que se fizer necessário.
Seguem-se outras regras: não passar o dedo sobre a superfície já preparada e uma vez preparada superfície, não deixá-la por muito tempo aguardando a fixação do extensômetro e sua posterior proteção. Em geral, este tempo deve ser de no máximo 20 a 30 minutos, conforme o material da superfície. Porém, se possível, quanto menos tempo, melhor.
Outra regra importante é nunca colocar os dedos nos extensômetros, especialmente na face inferior. Toda a manipulação deve ser feita com pinça, cuja ponta deve ter sido previamente desengordurada.
Os materiais usados na limpeza da superfície devem ser da mais alta pureza, de tal forma que não tragam resíduos.
Como materiais de limpeza recomenda-se algodão hidrófilo e gazes de qualidade medicinal, e papéis absorventes puros, que não contenham outros produtos a ele incorporados, como perfumes, etc.
Outra prática é remover os produtos de limpeza utilizados na superfície que foi limpa antes da sua evaporação, retirando, desta forma, os contaminantes que este produto de limpeza dissolveu; provavelmente estes contaminantes não irão se evaporar junto com o produto, recontaminando a superfície.
Também é muito importante, ao se friccionar uma superfície com um material de limpeza, faze-lo sempre numa única direção, de modo a levar a impureza para fora da área, e não efetuar movimentos de vai e vêm, ou circulares, que podem remover a impureza de um ponto e recontaminar outro.
Finalmente, aconselha-se a sempre descartar os materiais de limpeza (gazes, papéis absorventes, algodão, etc.) após terem sido usados apenas uma única vez, seja na limpeza da superfície, ou mesmo de alguma ferramenta.
É oportuno destacar que quando a peça está contaminada por silicone, contido em graxa ou outros produtos, tem-se um caso mais trabalhoso de preparação, pois o silicone é difícil de detectar e de remover, e por sua vez impede a atuação do fixador. Portanto, a melhor prática é sempre evitá-lo.
A preparação da superfície está dividida numa sequência de sete etapas, a serem obedecidas na ordem descrita abaixo e que pode apresentar variações conforme o material da superfície e sua eventual reação com desengraxantes e produtos químicos, mas que, de modo geral, é válida para os mais diversos metais, vidros, cerâmicas, plásticos, etc. Um caso especial, devido à porosidade apresentada, é a preparação de superfície de concreto.
ETAPA 1 – DESENGRAXAR
É sempre a primeira operação, para evitar que nas etapas seguintes, contaminantes penetrem na superfície. A área desengraxada deve ser de dimensões razoáveis para evitar eventuais recontaminações das vizinhanças, por qualquer descuido. No desengraxamento pode ser usado qualquer produto desengraxante que seja eficiente.
ETAPA 2 – LIXAR A SUPERFÍCIE
É para a remoção de tintas e outros revestimentos superficiais, como os obtidos em galvanoplastia (niquelação, cromação, etc), remoção de ferrugens e oxidação. Destina-se também a proporcionar um bom acabamento da superfície, que, quanto mais perfeito, melhor para a precisão dos resultados. A granulometria das lixas a serem usadas depende, caso a caso, do estado da superfície. Normalmente é uma série de lixas de granulometrias diferentes, partindo-se da mais grossa para a mais fina. Genericamente recomenda-se uma sequência de lixas d’água nºs 180, 280 e 400. Pode-se também usar jato de areia de alumina ou óxido de silício de granulação bastante fina, mas é importante observar que o ar do compressor seja isento de óleo e umidade.
ETAPA 3 – LIMPAR E DESENGRAXAR NOVAMENTE
Para a remoção dos resíduos da etapa anterior.
ETAPA 4 – LIXAR A SUPERFÍCIE
Usar lixa d’água 400 ou 600, uniformizando a superfície.
ETAPA 5 – MARCAÇÃO DO LOCAL DO EXTENSÔMETRO
O extensômetro possui marcações apropriadas para a sua centralização.
Localiza-se o ponto exato onde deve ser colado o extensômetro e traça-se, na superfície da peça, dois riscos perpendiculares, que irão se cruzar exatamente nesse ponto. Estes riscos deverão coincidir com as marcações do extensômetro, quando da sua colagem. Os riscos poderão ser feitos com lápis preto duro ou esferográfica.
ETAPA 6 – APLICAÇÃO DO CONDICIONADOR
O objetivo é remover possíveis oxidações superficiais. A aplicação pode ser feita embebendo-se a ponta de um cotonete no líquido Condicionador ou um papel absorvente. O cotonete deve ser rolado na superfície partindo-se do centro para as laterais, de modo e não trazer possíveis contaminações das laterais para o centro. Em seguida secar com papel absorvente, também com movimentos do centro para as laterais. Repetir 2 a 3 vezes até a limpeza completa (observar o estado do cotonete e do papel absorvente que foi usado, amarelado, ao retirar a oxidação existente).
ETAPA 7 – APLICAÇÃO DO NEUTRALIZADOR
A aplicação também deve ser feita com cotonetes, e a secagem com papel absorvente, tal qual na etapa anterior, repetindo-se a operação 2 a 3 vezes para assegurar a perfeita reação química de neutralização do Condicionador anteriormente aplicado, e trazer a superfície para uma alcalinidade própria para receber o adesivo.
FIXAÇÃO DO EXTENSÔMETRO
É executada com o auxílio de uma técnica simples e eficiente.
Previamente posiciona-se junto à área de trabalho um rolo de fita adesiva FK-1 em seu suporte. Esta fita deve estar com a sua extremidade desenrolada e estendida até a serrilha do cortador de fita.
Com uma pinça, o extensômetro é retirado da embalagem, a pinça não deve pegar por sobre a grade do extensômetro, mas somente sobre a base, digamos que do lado em que estão os terminais. O extensômetro é levado para sob a fita estendida colando-o apenas sobre uma mínima faixa da base do lado oposto ao da pinça.
A fita é cortada, deixando alguns milímetros além de cada lado do extensômetro, que nela está o preso.
O extensômetro, com a fita adesiva nele colada, é levado pela pinça, até o local em que deverá ser fixado. É posicionado, fazendo-se coincidir exatamente os traços de marcação feitos na superfície da peça com as marcações para centralização do extensômetro, quando então a fita adesiva é fixada na peça mediante ligeira pressão. O extensômetro, portanto, fica preso à superfície da peça apenas por um de seus lados, através da fita adesiva, como uma página de um livro.
Levanta-se o extensômetro, como se fosse virar a página do livro, aplicando o fixador escolhido na superfície da peça no lado inferior do extensômetro, conforme instruções próprias de cada produto.
Com uma película de teflon por sobre o extensômetro ele é virado e encostado na peça com a pressão dos dedos.
Sobre o teflon coloca-se uma almofada de borracha de silicone, que é presa ao local com a fita adesiva FK1.
Aplica-se uma pressão e um aquecimento por um determinado tempo, conforme as instruções de cada produto, após o que retira-se a almofada de borracha silicone e a película de teflon. Retira-se a fita adesiva FK1 com uma pinça, levantando cuidadosamente uma de suas pontas e puxando-a, tal que a fita forme um ângulo bastante agudo com a peça.
Conforme a finalidade do ensaio a ser feito e a forma e dimensões da peça, temos um fixador recomendado e um determinado processo de cura. Isso pode introduzir pequenas variações no procedimento acima, facilmente dedutíveis e definir métodos para se aplicar a pressão e aquecer a peça.
EXTENSÔMETROS COM CONECTOR
Ao se proceder a ensaios e análises com o emprego de extensometria, muitas vezes se depara com trabalhos a serem executados em estruturas grandes e complexas, onde são inúmeros os pontos onde devem ser aplicados os extensômetros.
Daí resultam inúmeras dificuldades na instalação e conexão dos extensômetros ao instrumento de leitura.
Exemplificamos:
• o acesso aos diversos locais específicos;
• a falta de espaço, que ocorre, de modo geral, pela concentração de pontos a ensaiar em pequenas áreas;
• espaços para o posicionamento de terminais de ligação;
• a necessidade de executar pontos de solda para conexões, em posições incômodas para a tarefa;
• a grande quantidade de cabos elétricos envolvidos, a serem identificados um a um com seu respectivo extensômetro, e o correspondente canal de entrada no instrumento de leitura, por vezes localizado à distância, e as passagens destes cabos.
Por outro lado, observa-se que em todas estas situações a fixação dos extensômetros se da com a utilização de produtos que atuam à temperatura ambiente; isto é, não ocorre a danificação de um conector pré instalado, o que ocorreria caso fosse necessário a utilização de temperatura para a cura do fixador.
Com o objetivo de simplificar e facilitar o trabalho de instalação e ligação dos extensômetros ao instrumento de leitura, a EXCEL SENSORES apresenta a opção de fornecer os extensômetros já dotados de conectores elétricos.
Assim, os extensômetros apresentam-se com 25 mm de fios de cobre esmaltados, eletricamente isolados, soldados em seus terminais de ligação, tendo na outra extremidade o conector macho 180 0 , nas alternativas com 2 vias ou 3 vias, caso a ligação a ser feita seja com 2 ou 3 fios. Na codificação dos extensômetros são as opções C2 e C3; na possibilidade dos extensômetros também serem encapsulados, as opções serão ENC2 e ENC3.
Quanto ao lado do cabo elétrico, devem estar os correspondentes alojamentos com os terminais para conector fêmea, que a EXCEL SENSORES oferece dentro de sua linha de Acessórios, no tópico Terminais de Ligação.
Quando da sua utilização, recomenda-se que imediatamente após a colagem de cada extensômetro, com o mesmo adesivo, se proceda também à colagem do conector a ele ligado; a seguir, com a proteção do extensômetro com a Resina Silicone RK, esta seja estendida aos fios de cobre entre o extensômetro e o conector, proporcionando-lhe maior segurança mecânica ao se manipular nas áreas vizinhas.
Nos terminais com 3 vias, observar quais são as 2 vias que estão ligadas entre si, para proceder à correspondente conexão no instrumento de leitura.